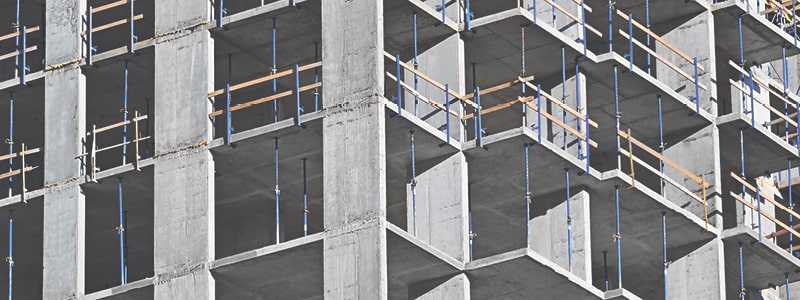
Modern Methods of Construction
The construction industry is often accused of not achieving levels of productivity gain and progress over the last 50 years, when compared to many other industries, in particular manufacturing. The manufacturing industry is a relevant comparator to urban building construction, given that urban building construction is effectively the manufacturing of buildings.
However, there have been significant gains achieved in the last fifteen years in the urban building construction industry, through the adoption of what is collectively termed “modern methods of construction” – abbreviated to MMoC. It is sometimes also referred to as DfMA – Design for Manufacture & Assembly.
We are proud to be a global industry leader in the development and engineering of solutions utilising modern methods of construction.
MMoC is the adoption of design and construction strategies and approaches that are inspired by modern manufacturing techniques and processes, and that seek to reduce cost, reduce construction time, improve construction quality, and improve the functionality and value of completed buildings.
There are several key principles that are commonly applied to projects in the process of adopting MMoC; it should be noted that some of these are design principles - not construction principles - as the ability to apply MMoC is critically connected to the development of design.
(Click Table to Enlarge)
Our specialist understanding of both structural design and construction methodology and logistics has helped us become an industry leader in the development of solutions that adopt MMoC, as well as digital tools to assist in the adoption and delivery of projects utilising MMoC.
This experience has led us to achieving a number of industry MMoC milestones, including:
- Australia’s tallest tower utilising precast concrete walls (52 storeys) in 2007
- The world’s tallest mass timber building (9 storeys) in 2012
- The delivery of over 110 precast 3-storey buildings for the Australian Defence Force
- Several 2D (flat pack) and 3D (volumetric) modular systems including but not limited to Unitised Building, Rush and Autobox.
- Melbourne’s first fully volumetric private apartment buildings, in circa 2008
- 1,400 beds of student accommodation in Sydney, in buildings up to 10 storeys in height that were fully precast offsite.
Our modular experience started in Australia where Unitised Building (UB®), operated under licence by the Hickory Group, worked together with Fender Katsalidis (architects of the UB® System) and us (engineers of the UB® System) to deliver an innovative structural building technology system. The UB system is essentially a structural steel frame infilled with lightweight foamed cement to provide fire rating, acoustic, and thermal insulation. Structural concrete is limited to a 50mm wearing screed on the floor panels.
The resultant building structure weighs 40% of a normal reinforced concrete structure.
We were responsible for the design of all the structural elements, including the module-to-module connection systems. The benefit of the UB™ System was unprecedented design flexibility, façade and structural configurations, with no fixed module height or width. The system could adapt to the specific design features of any given project, allowing it to follow, not dictate, architectural design. The system was also developed as a panelised solution, referred to as Rush.
Our modular solutions have recently expanded with the launch of Autobox – a transforming volumetric modular system that can be applied to almost any building design, and offering unprecedented cost, time and sustainability advantages. Visit our Autobox page for more information.
Modular buildings are perfectly suitable to embrace digital technologies. The rules and patterns that generate efficient design suit a Data Driver Design approach. The Data can be translated to any drafting or analysis software and can have a central source (excel or other databases). It can lean on computation design tools and techniques such as Genetic Algorithms, Generative Design and algorithmic processes. The creation of a standard library of members/components and details can greatly automate the drawing delivery, as well as speeding up production, assembly and reducing costs and risks.
We have developed digital tools which will allow clients instant access to Project model data, such as steelwork tonnages, concrete volume and embodied carbon, as well as useful information from the model
such as heaviest framing element to inform crane strategy and design.
We also use these tools internally to audit the models and ensure the BIM Data within our models meets our internal BIM standards as well as any client specific EIR’s. We can also appraise our design efficiency and spots errors and inefficiencies more easily than with traditional tools.
The study of site logistics is critical for the adoption of modern methods of construction. Since most elements would be fabricated offsite, studies with regards to transport, lifting and installation sequence of prefabricated elements could immediately indicate the feasibility of utilising these methodologies. It is essential that these studies should be carried out early at the design phase to ensure feasibility of the scheme for the existing site.
Want to adopt MMoC on your project? Ask us.
At Robert Bird Group, we offer an early-project-phase consulting service, where we assess your project’s suitability for design and delivery whilst enjoying the benefits afforded by modern methods of construction. This service is available whether we are the design engineering consultant for the project, or not. Contact us to find out how your project can benefit from the latest in construction technology and methods.